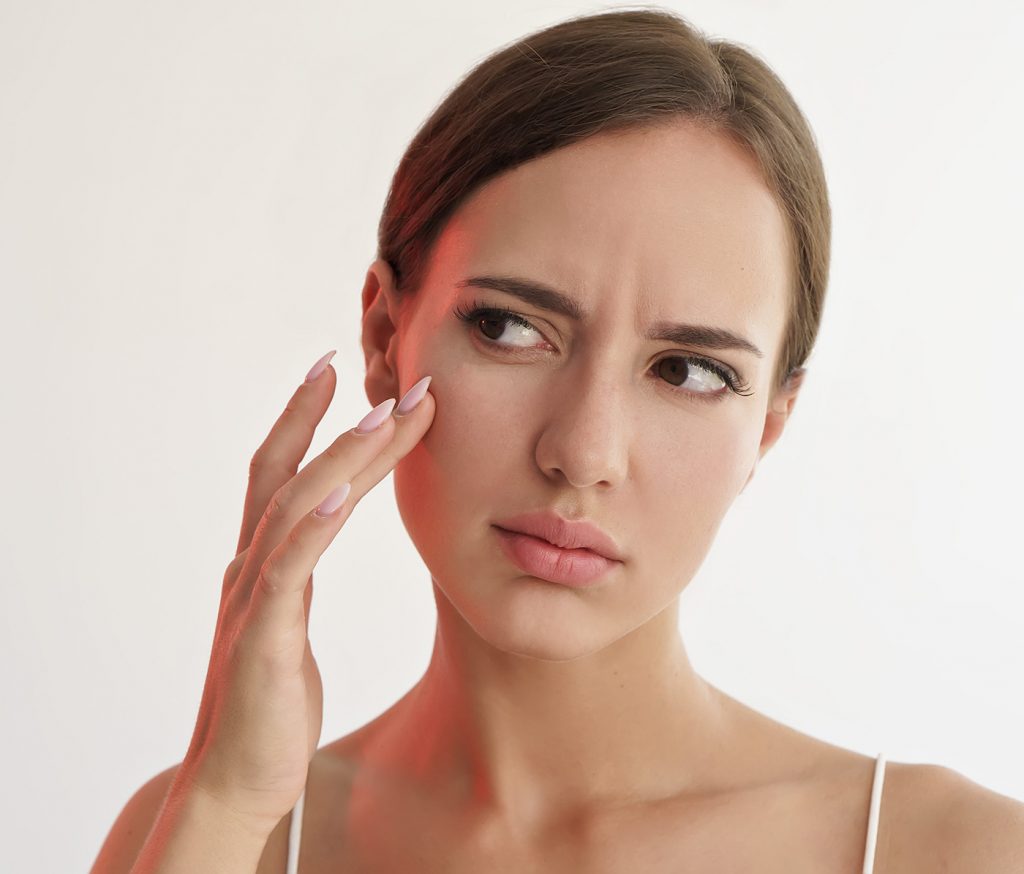
Meeting with Fabio Mazza, Operations Manager at San.eco.Vit.
San.eco.Vit. main idea is to add something to the planet.
“If you produce with industrial materials, you are definitely taking something away from the planet. While we try to produce with recycled materials, raw materials of natural derivation, with something that the planet has produced in its time, also considering those of reform, in respect of what is welcoming us and allows us to live.”.
Fabio Mazza, Operations Manager at San.Eco.Vit.
“The idea that drives this Group is to promote a natural lifestyle, even within us, encouraging not to print, not to consume plastic bottles, to contain waste….
We want to have a clean, essential company, in line with what we offer, that is why San.eco.Vit. gives within itsel the idea of what it wants to be: an organic company, healthy and green, which achieves something more exceptional than the standard.
A company in Brianza, surrounded by green, which pays attention to the natural, but also to technologies that can help to better develop the product, communication and the relationship with the customer. A company that respects the environment and the laws, that works with coherence in order to realise products with determined requirements and certifications that attest the absolute quality of the product.
“The certifications of San.Eco.Vit. are not meant as the annual achievement of a goal, but they are practised daily, applying daily principles in line with what we want to be. So our certifications are a daily prize for what we do every day.
It is a great satisfaction whenever customers and auditors recognize it, they see that we have created something new and improved formulas consistently, also following the observations made by the customer himself. Obviously, the achievement of certifications such as IFS HPC, however at the highest levels, is a factor of pride and an important milestone because it attests the production quality of the entire supply chain.
In San.eco.Vit. the continuous improvement of the company is also a daily exercise.
“The company wants to be virtuous, so everything is done according to the principle of Total Quality Management and sustainable procedures, in compliance with ECO environmental certification.
We are currently strengthening all departments, production and filling departments, investing in new software, machines, equipment and new resources.
“In the production we look for materials that come from the world of recycling and recyclein our turn, we select where possible suppliers close to us, natural and innovative raw materials, certified and certifiable.
In the plants we have devices for heat recovery, so the energy spent in the production part is reused for heating the company, and all the lighting is LED.
The spaces are equipped with timers for temperature control and automatic shutdown of air conditioners for energy saving. Finally, the integrated logistics allows us to have fewer goods that travel on wheels, therefore toreduce our CO2 emissions, but also to share good practices such as the reduction of packaging materials, used in an increasingly sustainableway.
“At the same time we are working on the development of the entire IT part related to communication and sales channels, to optimise flows and processes.
We are improving the internal management of the Naturalia Tantum Group and the integrated logistics system, which we have unified into a single pole.
Following identical procedures for all the companies of the Group, having the centrality of the data, the same logistics system and the same purchasing methods allows us to best manage quality, processes, product certification, and to create excellent synergies between the companies of the Natural Pole, to strengthen the role of Naturalia Tantum as a primary national and international player for natural cosmetics and bio, nutraceutical and natural integration.
Continuous improvement also involves constant training.
“Training is a constant activity, also conducted internally to be competitive and innovative, especially in a very dynamic and evolving sector like ours.
After an analysis of the needs, we choose the best interlocutors to deal with the topics in a comprehensive manner: University, Regulatory Consultants, External bodies that have the best skills and characteristics compared to the topic that each time you are facing.
People in San.eco.Vit are at the core of every project.
“People give added value to any procedure, they know well what they do in everyday life and, with critical sense and skills, they contribute to continuous improvement.
Then comes the technologies and innovations that allow to create a better product and offer a higher safety to the customer.
This circle of skills, virtues and continuous improvement allow to bring to the international market excellent products that give new luster to the made in Italy, bringing wealth and work, positioning San.eco.Vit. as a resource for the Italian territory that operates in an ethical and sustainable way.
Fabio Mazza, Operations Manager, is a reference point for the corporate life of San.eco.Vit. It follows all activities related to the plant, purchasing and procurement, production, IT, management, systems and training, HR management, logistics, taking care of compliance with the rules and protocols.